Whether you’re renovating your home, building your dream office, or preparing a commercial space, you will expect its floor to be an even surface that is not only functional but visually flawless.
For homeowners and businesses alike, floor screeding is an investment in quality, comfort, and peace of mind. It helps prevent noticeable dips, bumps or sloping areas which make the space uncomfortable to walk on. That’s where floor screeding plays a major role. In this blog, you will get a detailed overview of floor screeding.
What is Floor Screeding?
Floor screeding is the process of applying a screed mixture of cement, sand and water in the subfloor to create a smooth and levelled surface. They are highly durable, having the ability to withstand loads, foot traffic, heating and other impacts.
In general, screeds are made of cement, sand, and sometimes additives that are mixed with water to achieve applicable consistency. It is widely used in residential, commercial, industrial and renovation purposes.
Types of Floor Screeds
Bonded Screed
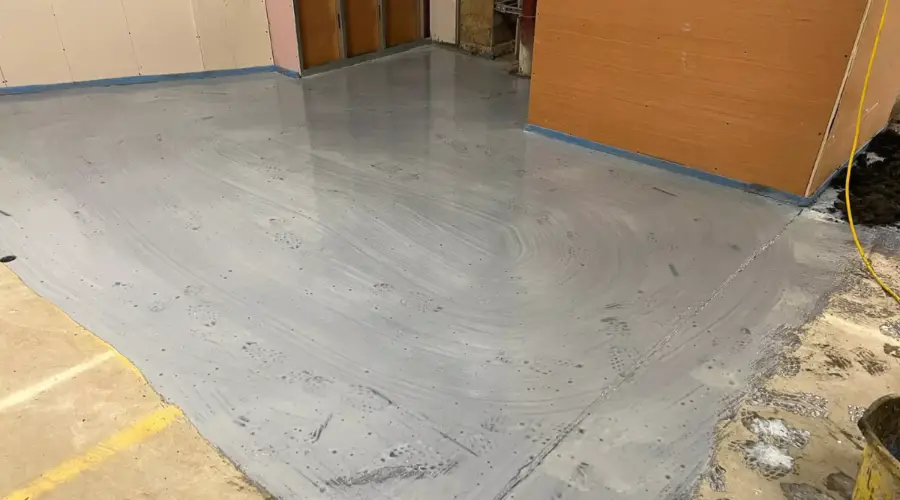
The bonded screed is directly applied to the solid substrate using a bonding agent (adhesives) to ensure strong bonding. These screeds are usually 15 to 50 mm thick and are crucial in high-load bearing, and high traffic areas, such as driveways, parkways and heating systems with cast-in pipes.
Unbonded Screed
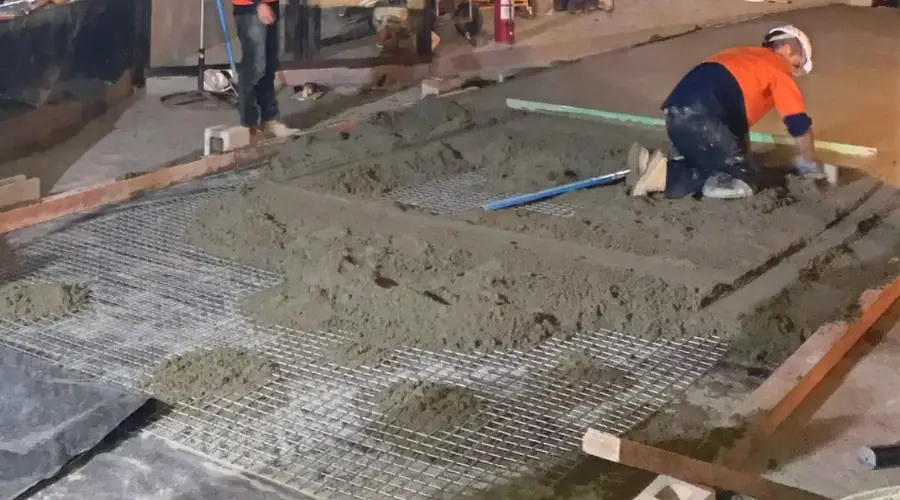
Unbonded screed is applied on top of a damp-proof membrane and is not directly bonded with the substrate to reduce shrinkage and moisture issues. These function the same as bonded screeds but are thicker, exceeding 50 mm.
Floating Screed
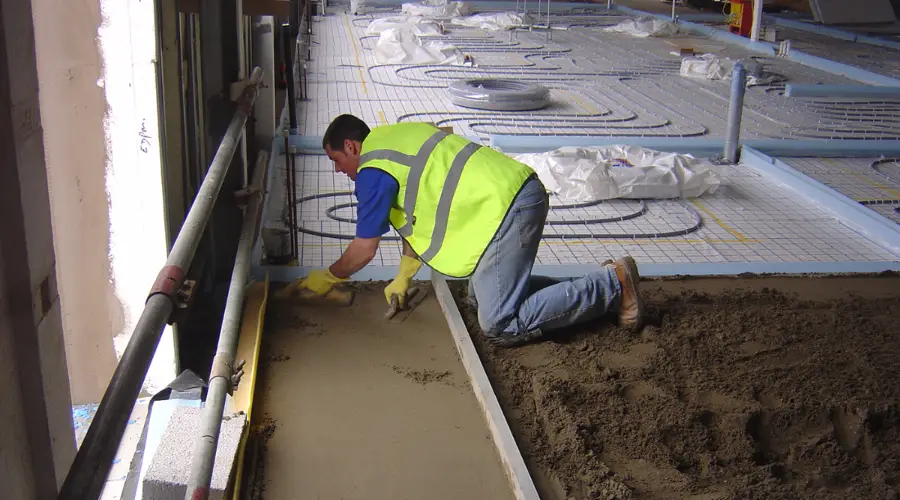
It is applied on top of insulation materials to provide better thermal and acoustic insulation to the structure. For this, the screed layer is usually thicker than the other two screeding types, i.e., around 65 mm. They are ideal for underground hearing systems, where insulation is crucial for energy efficiency.
Heated Screed
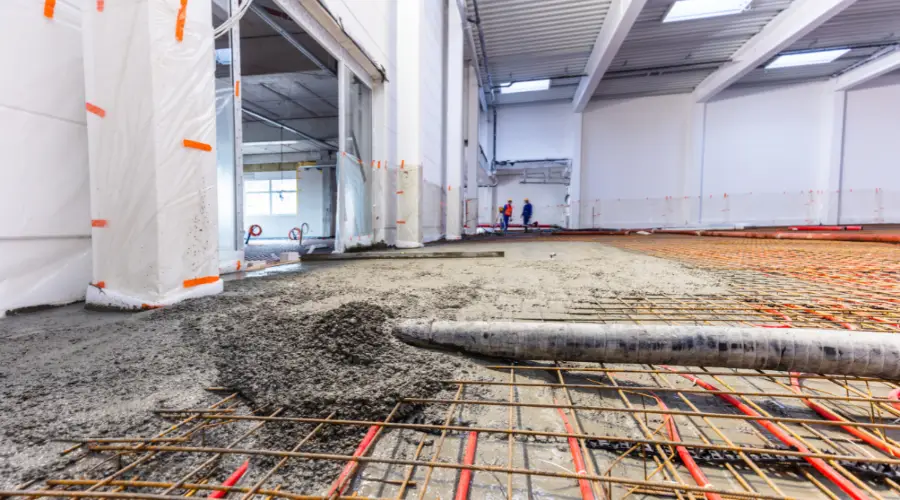
Heated screeds provide good thermal insulation to efficiently transfer heat to the floor surface and are ideal for underfloor heating systems to prevent damage caused by heating pipes.
Materials Used in Floor Screeding
The materials used for screeding include cement, clean and sharp sand, water, and other additives to achieve specific properties. Usually, polymers, metal mesh or glass materials are used to reinforce the floor screedings. These materials are blended adhering to local standards and proportions, based on thickness.
To achieve screeding thicknesses of less than 40 mm, the cement-sand ratio should be either 1:3 or 1:4.5. For more than 40 mm, the cement-sand-coarse aggregate ratio should be 1:1.5:3.
Floor Screeding Process
Preparing the Surface
Inspect the substrate flooring surface to ensure a clean and moisture-free surface. Provide a damp-proof membrane if necessary to prevent the structure from potential moisture damage. After initial inspections, divide the floor into sections using straight timber battens to maintain consistent thickness. In the case of bonded screeds, roughen the concrete surface and coat bonding agents for proper adhesion.
Mixing and Laying
Prepare the screed mix using cement, sharp sand, water and other additives at an appropriate ratio, to bring it to the proper consistency. Pour the screed mixture into small sections and spread it uniformly across the sections using a trowel.
Levelling
After laying, compact the screed using a screed board or float to remove air pockets and ensure an even finish. After compaction, use a straightedge across the surface of the screed in a sawing motion to make the floor surface achieve a smooth and levelled surface.
Curing
Allow the screed to cure properly by keeping the surface idle and free from heavy loads and traffic to achieve full strength and efficiency. Make sure the surface remains wet for a few days, so that it can gain adequate strength.
Importance of Proper Floor Screeding
- It is essential to provide a smooth and level base for different flooring types, and effective installation of materials.
- High-quality screed layers help in the effective distribution of loads uniformly across the surface, and in maintaining the structural integrity of buildings.
- It plays a major role in underfloor heating systems to conserve energy and reduce heating costs.
- It acts as a barrier against moisture by protecting the substrate and flooring.
- Properly screeded floors help in minimising the maintenance cost spent on repairing and replacements.
- High-quality screeding provides a smooth and flat finish, improving the overall look.
Common Mistakes in Floor Screeding and How to Avoid Them
Insufficient Surface Preparation
Preparing the surface is necessary for any construction process, as it plays a vital role in determining the quality and efficiency of the finished product. Similarly, poor or inadequate surface preparation affects the bonding. This can be addressed by giving additional care for cleaning and removing the impurities from the surface, and repairing cracks using binding materials.
Poor Mixing Ratios
Incorrect or poor mixing ratios of screed could affect its strength, causing damage to the structural integrity. This can be prevented by following the mixing guidelines suggested by the manufacturer or by using pre-mixed screeds.
Poor Application
Poor application of screed could result in uneven surfaces and loose surfaces filled with air pockets. This can be addressed using proper tools and techniques to spread the screed and providing adequate compaction during installation.
Screed Shrinks
Screed layers shrink when they dry and this could cause small cracks within the surface. This can be addressed by adding polypropylene fibres or edging foam to the mix to minimise shrinkage.
Cracks
The development of micro-cracks is one of the most common issues in screeding, which are often caused by a rushed drying process. This can be prevented by keeping the room under stable humidity and temperature conditions throughout the curing process.
Innovations in Floor Screeding
- Laser Screed Technology uses laser-guided systems to provide precise levelling of concrete that can minimise errors and enhance the quality of the finished product.
- 3D Printing Technology is used to create intricate and customised design patterns, allowing greater design flexibility and offering unique floor designs.
- Automated Screeding Robots use advanced sensors and algorithms to automatically spread and level screeds precisely without the need for manual labour.
- Rapid Drying and Curing Screeds reduce the drying and curing time, thereby improving the construction speed.
Conclusion
Floor screeding is a basic construction practice in providing strong, high-quality, smooth and durable flooring surfaces. Proper screeding prevents the structure from cracking and water penetration, helps in uniform load distribution and provides thermal insulation and longevity of the structure.
FAQs
In specific, there is no ideal thickness for screeding as it varies based on its type, but it typically ranges from 25 mm to 100 mm.
Yes, you can. Underfloor heating can be installed employing any type of screed due to its thermal properties and installation characteristics.
Some common signs of poorly applied screeds are cracking, uneven surfaces, moisture problems, poor bonding with the substrate, and the development of air pockets.