With the rise in building construction, the demand for sand at construction sites has also grown significantly. To meet this increasing demand, industries have begun manufacturing sand. Crushed sand is made artificially by crushing large igneous rocks, granite, and other stones. A fixed sieve provides homogeneity in the sand, while proper production processes decrease the chance of adulteration. To protect natural resources, crushed sand is produced as an alternative to fulfil construction needs. Let us see more detailed information about crushed sand, such as types, properties, applications, advantages, and disadvantages.
What is Crushed Sand in Construction
Large stones are crushed into tiny pieces, which are subsequently cleaned and graded to produce crushed sand, an artificial substance. It is suitable for concrete, brick, and blockwork and is mostly used in mortar and concrete mixtures as an alternative to natural river sand. Other names for crushed sand include M-sand, crushed stone sand, artificial sand, and pozzolan sand.
Types of Crushed Sand
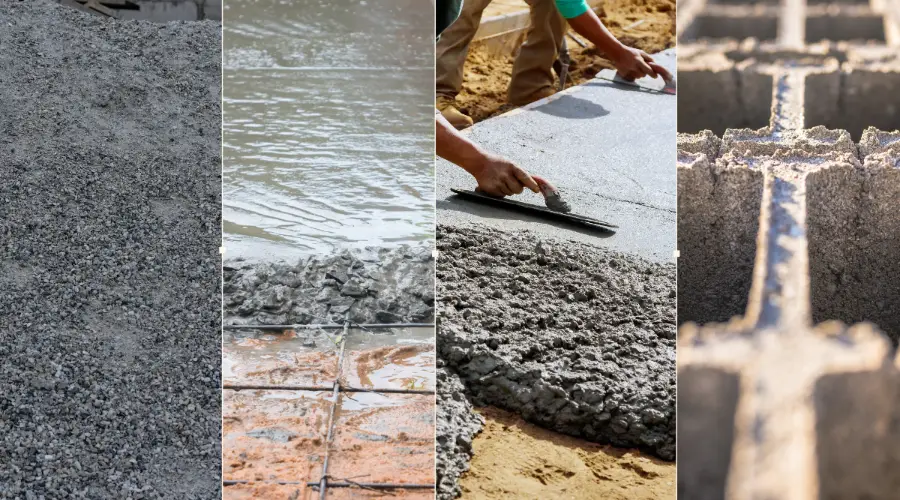
The following are the several types of crushed sand (M-sand):
Crushed Sand for Concreting:
For concrete applications, the granules range in size from 150 microns to 4.75 millimetres. It must comply with IS Code 383:1970.
Crushed Sand for Plastering:
Crushed sands are ideal for tiling and wall plastering, the granules range in size from 150 microns to 2.36 millimetres and comply with IS Code 1542:1992.
Crushed Sand for Brick or Block Work:
Crushed sands are specifically designed for masonry, brick, and block-laying projects.
The Granules range in size from 150 microns to 3.55 millimetres and comply with IS Code 2116:1980.
Properties of Crush Sand
S.No | Properties | Description |
1 | Manufacturing process | Large aggregate pieces, boulders, or stones at a quarry or mill are crushed to create crushed sand. |
2 | Shape | Angular or cubical |
3 | Texture | Hard or rough |
4 | Dry density | 1.75 kg per cubic m |
5 | Particles passing 75 microns | Up to 15% (IS: 383 – 1970) |
6 | Specific gravity | 2.73, depending on the parent rock |
7 | Adulteration | Fewer impurities |
8 | Applications | In comparison to river sand, it is highly recommended for RCC, brickwork, and blockwork. |
9 | Environmental impact | Eco-friendly compared to natural sand. |
Application of Crush Sand
Greater Strength Concrete: Crush sand is an effective alternative building material to river sand. It is the perfect material for construction since it is made with exact gradation and suitable physical characteristics including shape, smooth texture, and consistency. By lessening problems like segregation, efflorescence, gaps, and capillarity, its physical characteristics increase the strength of concrete.
Increased Durability: Made from premium granite, crushed sand has regulated chemical and physical characteristics that make it appropriate for use in concrete construction. By lowering permeability and moisture intrusion, these characteristics assist concrete structures to withstand severe weather conditions, prolong their lifespan, and stop steel corrosion.
Better Workability: Crushed sand has dimensions, forms, and textures that make the concrete easier to work with. Its regulated physical characteristics make concrete more effective and workable by lowering the amount of cement and water required to bond with coarse particles.
Advantages of Crush Sand
- Crushed sand has more compressive and flexural strength than natural sand because it is graded properly and has a higher fineness modulus.
- While it is devoid of silt, dust, and clay, the particles are packed more densely, making the concrete stronger.
- It is produced close to building sites, which guarantees a consistent supply and lowers transportation costs.
- Crushed sand is appropriate for high-quality concrete because of its perfect shape, smooth texture, and uniform gradation.
- Even in severe climates, durability is guaranteed by well-balanced physical and chemical characteristics.
- It reduces holes, steel corrosion, segregation, honeycombing, and other flaws in concrete.
- Strength and durability are increased by the smooth, cubical texture produced by VSI shaping machines.
- Concrete workability and mortar flexibility are enhanced by appropriate gradation and cubical particles.
- It solves environmental issues and is a sustainable substitute for river sand.
- It has a larger unit weight, less permeability, and superior scratch resistance because it is silt and clay-free.
- It is affordable, readily available close to locations, and lowers transportation expenses.
Disadvantages of Crush Sand
- Improperly crushed angular or flaky particles require more cement and water, which makes them unsuitable for concrete.
- Crushed sand is more costly than river sand in some places, such as West Bengal, due to inadequate crusher setups.
- Costs may increase because high-grade pumpable concrete for tall buildings needs more cement using M-Sand than river sand.
The Manufacturing Process of Crush Sand
The crushing of granite rocks produces crushed sand, which is also known as M-sand in general. Crushers smash coarse rock deposits, separating the resultant material into various sizes. Sieving and washing further refine the sand, removing tiny particles and contaminants.
Steps in M-Sand Preparation
- Extraction and Aggregate Crushing
- Screening, sorting, air classification, and storage/handling
Manufacturing Process:
- The first stage involves crushing stones of various sizes into aggregates using Vertical Shaft Impact (VSI) crushers.
- During the second stage, the aggregates are treated in a Rotopactor to yield sand with the desired grain size.
- In the final stage of manufacturing crushed sand, dust is screened out, followed by washing to remove tiny particles, resulting in a clean M-sand.
- Cleaning guarantees that the fraction of microfines (particles smaller than 75 microns) is less than 15% by weight. The washing procedure also keeps the resulting sand moist or partially wet, reducing water absorption during concrete manufacturing. This enhances the concrete’s work capacity and strength.
Conclusion
Environmental problems like erosion of rivers and coastlines and pH changes are brought on by the illegal large-scale exploitation of natural sand. Crushed sand, also known as manufactured sand, offers a sustainable alternative because it is free of impurities like silt, clay, organic matter, and soluble elements that could reduce its strength and durability. Crushed sand requires energy to create, but it can be generated locally, saving money on transportation and reducing environmental effects.
FAQ’s
Crushed sand can be used as a substitute for natural sand. It is made by crushing and grading granite stones and boulders, resulting in manufactured sand, also known as crushed sand or stone dust. This artificial sand serves as an alternative to the natural sand sourced from riverbeds.
Crushed sand, sometimes referred to as manufactured sand or M-Sand is a fine aggregate made by breaking up big rocks and stones into smaller pieces.